Automation results in significant completion efficiency gains in Delaware
As West Texas operator Primexx Energy Partners has pursued an aggressive program to delineate and develop its Delaware basin acreage in Reeves County, the company has leveraged new technology to increase the efficiency of completion and stimulation operations and achieve significant cost-savings. Downing’s new Freedom Series Completion System (FSCS) has been a key factor in helping Primexx significantly reduce the number of days on location by increasing stages per day by 20% to 60%, resulting in major cost reductions and time savings.
PRIMEXX OPERATIONS
Primexx is a privately held independent operator, focused exclusively on developing Wolfcamp shale reservoirs in the Delaware basin. The company holds leases on approximately 42,000 acres and produces 20,000 bopd and 40 MMcfgd, up from 500 bopd and 2 MMcfgd in 2017 when it launched its development campaign with investment from the Blackstone Group. Primexx’s drilling campaign keeps two to three rigs operating continuously, and at least one frac crew is dedicated to completing its wells. The company has installed more than 400 mi of water and gas gathering pipelines. Two water treatment facilities provide 80,000 bpd of recycled water, and compression stations deliver gas to high-pressure gas sales pipelines.
Delaware basin formations require higher-pressure fracs than those in the central Midland basin. Frac pressures are as high as 13,500 psi and average at least 10,500 psi throughout the pumping process. To control the pressure, Primexx uses frac stacks rated at 15,000 psi. Such high-pressure operations are a demanding application for the frac pump fleet, so it is important to keep sufficient pump horsepower operational to complete each stage. And for Primexx, the most important efficiency goal is to optimize frac fleet horsepower.
EARLY TECHNOLOGY ADOPTER
“We are a small company with just 50 full-time employees, so we are a fast mover on adopting technology to improve efficiency,” said Primexx COO Sam Blatt. “We rely on industry partners and are very selective in choosing suppliers like Downing, who share our approach and commitment to safety and operational efficiency.” Phillip Douget, Primexx manager of integrated service planning, added, “Higher technology has a higher unit price, but it creates operating efficiency that saves more money than the incremental cost.
Ongoing efforts to improve efficiency have included adopting zipper manifolds to frac two or more wells in sequence; greaseless (Teflon-coated) wireline cable that speeds wireline runs and eliminates the need for a grease trailer; and integrated, addressable perforating gun systems, which do not require on-location assembly. Ball-in-place composite frac plugs are used to eliminate ball drops after the first stages in the well’s toe. The pumping operation is automated, so that a computer controls how the pumps ramp up pressure, rather than by manual operation, improving efficiency and reducing fuel consumption. The company also uses innovative water management, field-wide infrastructure and water recycling to use 80% produced and flowback water in its pumping operations.
In 2018, Downing representatives, including company President Brian Wiesner, made a presentation to Primexx management that showed how the Freedom Series Completion System could significantly improve plug-and-perf completion operations. “Downing showed that they could reduce wireline swaps that usually take 45 min. to less than five minutes, while reducing safety risk to personnel,” said Blatt. “We decided to use it on our next well.”
By summer 2019, Primexx used the completion system on 15 single- and multi-well pads, including a five-well pad in Reeves County. In each case, the FSCS enabled Primexx to achieve significant operational improvements on their plug-and-perf completion program.
“Increasing drilling efficiency used to be the big deal, but now efficiency in drilling long horizontal wells has reached its limit, until some new technology breakthrough comes along,” said James Wilhoit, drilling and completion superintendent, Primexx. Completions is where the savings are to be had now. Frac jobs can cost $600,000 to $700,000 per day. Our biggest challenge is optimizing the available horsepower to pump continuously and finish the frac job as quickly as possible.” Wilhoit added, “Even if the operator is paying the pumping supplier on a per stage basis, there are many related ancillary costs for every hour spent with equipment and people on location.”
INEFFICIENCIES OF PLUG-AND-PERFORATE COMPLETIONS
The plug-and-perforate technique is the most prevalent completion method in North America’s shale and tight oil plays. The method provides the ability to pinpoint fracture locations with perforating guns; adjust stage spacing during the completion; achieve zonal isolation between stages; and complete a hundred or more stages in a horizontal well.
While preferred, the traditional plug-and-perf method is highly inefficient and requires personnel to work at height in the red zone. Traditional wireline tool deployment involves three steps. First, the working valve on the frac tree is shut manually by a red zone operator. The wireline operator picks up the gun assembly and suspends it over the frac head and the red zone operator. Next, the red zone operator installs the wireline lubricator, which is pressurized using a backside pump. The frac iron is then pressure-tested, and if successful, the working valve is opened, and the wireline tools can be lowered into the well. This process takes 30 to 45 min. If the test is unsuccessful, more time is required to find and repair leaks in the iron.
Pulling the wireline tools after perforating is equally time-consuming, taking 30 to 45 min. per stage. The red zone operator closes the working valve manually, releases the lubricator, and bleeds off pressure. (At this step, closing the valve on the wireline can cut the wireline, resulting in a costly fishing job and at least a day of non-productive time or NPT.) If a ball is needed, the red zone operator drops it onto the swab valve and then installs the frac head cap. The frac iron is then pressure-tested, and if successful, the red zone operator manually opens the swab valve to let the ball descend down the wellbore and seat onto the frac plug to begin pressure pumping.
“There is a lot of time wasted between frac operations and wireline runs,” Blatt said. “This adds up to several days per well, and throughout a year, it totals several weeks of wasted time.”
COMPLETION SYSTEM INNOVATIONS
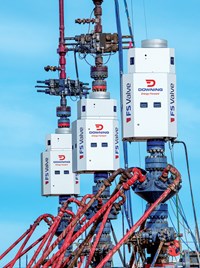
The FS Completion System (FSCS), Fig. 1, was designed to greatly improve the efficiency and safety of handling wireline tools during plug-and-perf operations. Placed between the frac head and the lubricator, the system is comprised of a multi-chamber valve, a quick connect latch, and an automated ball dropper. The hydraulically actuated valves create three chambers that are remotely operated via computer from a control cabin. The quick-connect latch enables the lubricator to be attached to the frac tree without personnel working at height in the red zone. In addition, the control cabin includes a hydraulically powered greasing unit that lubricates the zipper manifold valves remotely, further reducing red zone operations.
During each stage of completion, the multi-chamber valve equalizes pressure between the surface/lubricator and the well, and enables wireline-conveyed tools (as well as balls and collets when needed) to enter a pressurized wellbore. The FSCS achieves consistent equalization using fluid from the well and does not require a backside pump, Fig. 2.
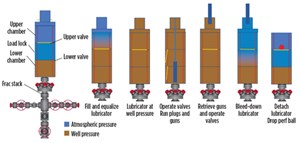
With the FSCS, wireline tools can be run in and out of the well without opening and closing the gate valve. This saves wear and tear on the gate valve, significantly reducing repair costs, as well as reducing greasing requirements. In addition, because the FSCS provides a dual barrier for well control, one hydraulic valve can be removed from the frac head, reducing height as well as the cost of the stack.
Without the stress of operation, gate valve failures are virtually eliminated. Replacing a gate valve can cause 12 hr of NPT. Downing reports that the FSCS has completed more than 4,500 stages without experiencing a gate valve failure on the frac stack.
When using the FSCS, there is no need to de-pressurize the frac iron between stages, as is required when using the gate valve to contain well pressure. Because the frac iron does not need to be re-pressured, no testing is needed, saving at least 30 min. per stage, allowing pumping to quickly resume on the next stage. In addition, frac iron leaks are significantly reduced from this reduction in pressure cycling.
With the new system, the lubricator can simultaneously attach to the quick-connect latch while the well is pumping. Once the stimulation process is complete on that stage, the lubricator equalizes to the well pressure, and the wireline is lowered to set the plug and perforate the next stage. This enables continuous pumping and significantly reduces stage to stage time.
The FSCS reduces wireline transition time to three minutes or less, compared to 30 to 45 min. using traditional methods, which on a 50-stage well can result in saving several days on well. Quick wireline swaps enable continuous pumping operations on zipper fracs, helping Primexx achieve its objective of maximizing available fracing horsepower on the well pad.
COMPLETING A FIVE-WELL PAD
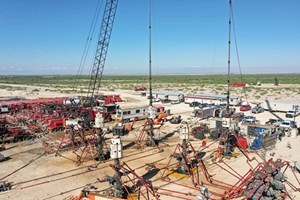
In early summer 2019, Primexx used the Freedom Series system while zipper-fracing five wells on a Reeves County pad. Five FS Completion Systems were attached to the five wellheads on the pad, Fig. 3. The wells were drilled to reach the target zone at approximately 10,200 ft, TVD, placing laterals that are 10,000 ft in length. The wells were then completed with an average of 50 stages, each. Well stimulations used slick water fracs, with approximately 500,000 lb of sand per stage, pumped at up to 85 bpm.
The pumping contractor supplied a fleet of 15 pumping trucks per fleet, plus two spare pumps for backup. On this project, the pad was divided into two sets of wells (with three and two wells, respectively) and was serviced by two frac fleets and two wireline units providing plug-and-perforate services. Completed using a zipper frac manifold for each well set, the wells were stimulated almost continuously, to reduce overall cost and bring the entire pad on production as quickly as possible.
Two FS control cabins were used to remotely operate the valves and latches on the two well sets. Using the two zipper manifolds, pumped fluid was redirected to a different well after each stage was pumped, alternately stimulating stages to perform zipper frac operations on all five wells in sequence. Wireline operations could be performed in one well in each set while pumping proceeded in another.
“Such highly efficient wireline operations make it more important than ever for the frac crews to keep pumps in operating order,” said Wilhoit. “Using the FSCS, the pressure to control NPT is shifted to the pumping crew from the wireline and plug-and-perf operation. When a pump goes out, they have to switch on one of the spares instead of stopping to repair the failed unit,” Wilhoit said. On jobs without the FSCS, there is typically an hour or more between stages to troubleshoot problems and maintain pumps. With the FSCS, there is no such delay, and the frac fleet can pump almost continuously, as long as enough horsepower is available. With 17 pumps per fleet on location and 15 needed for the frac treatment, a failed pump is taken offline and a back-up pump is activated to achieve the required horsepower without interrupting operations.
To take full advantage of the streamlined plug-and-perf operations, it is important to have well-trained people on location, who work in close coordination. “It’s a complex operation, with computers, specialized equipment, zipper manifolds and FSCS systems on every wellhead,” Wilhoit pointed out. “Everyone has to be kept on the same page to avoid mix-ups. The pumping, wireline and FS crews are in constant communication by radio, and no one goes into the red zone or adjusts a valve without clearing it with the company man. As long as everyone is properly trained, we can pump continuously. The new system reduces the number of people on site, reducing our cost and chance for error.”
SIGNIFICANT IMPROVEMENT IN STAGE EFFICIENCY
Since adopting the FSCS system, Primexx has achieved significant improvements in frac stimulation efficiency. “The FSCS system has completely changed the plug-and-perf process. On previous wells, prior to the FS system, we had 45-min.-to-1-hr wireline transition times,” Phillip Douget said. “With FSCS, it takes 3 to 5 min.”
Wilhoit pointed out that frac valve maintenance costs have been lower since the FSCS system’s introduction, and that no frac stack gate valves have needed replacement. Safety has been enhanced by eliminating the need for personnel to work at height while stabbing the lubricator and by removing the need to enter the red zone to open and close frac stack gate valves.
“In the past, we have used other systems to latch the lubricator to the frac stack,” Wilhoit added, “but they were twice the height of the latch on the FSCS, and took longer to make the connection. And unlike the other systems, the FSCS provides a double barrier to control the well, so we can place the lubricator on the frac head when the well is being fraced, so wireline work on the next stage can start quickly. That saves a few minutes a stage, and that time adds up.”
Most significantly, the FSCS has helped improve stimulation efficiency by as much as 60%. According to Douget, “We have gone from 3.75 stages per day prior to using the FSCS system to 5.0 stages per day on a single well, and 6.0+ stages per day on zipper fracs using the FSCS.”
“With the FSCS system, we can fracture more stages per day and stimulate more feet of lateral per day,” Blatt said. “And because we are on location for fewer days, we are completing our wells at a lower cost.”
Primexx expects ongoing improvements in efficiency as it continues to work with Downing. “We realize that the FSCS is not a static system and that it will keep evolving,” Phillip Douget said. “We encourage Downing to talk with our wireline and pumping suppliers to discuss improvements in the system and operating procedures to further improve efficiency.”
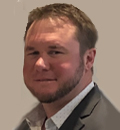
- To frac, or not to frac, that is the question (September 2024)
- U.S. drilling decreases on shale consolidation, technical advancements following record production (September 2024)
- Annular safety valves advance flexibility, reliability and safety in completion operations (July 2024)
- Dawn of a new day in completions (May 2024)
- Extracting resources from the Earth’s crust using multi-stage, fraced horizontal wells: First gas, then oil, now heat (May 2024)
- The five A’s on the road to completions automation (May 2024)