Proppant-sized solid inhibitors improve flow assurance in fraced wells
The economic value of a hydraulically fractured well is highly dependent upon flow assurance—that is, maintaining unimpeded flow of hydrocarbons from the formation to the surface. Flow assurance issues occur in hydraulically fractured wells, as a result of the deposition and buildup of naturally occurring particulates that are present in the system during hydrocarbon production.
Scale is one of several threats to flow assurance in these wells. Other threats include paraffin, asphaltene and gas hydrates. The severity of each threat varies by area, reservoir and system. The most prolific problems, which are seen often in systems producing high volumes of both water and oil, are scale and paraffin deposition. A well that is plagued by production interruptions caused by deposition of any of these substances loses considerable value, because of the cost of both remedial operations and lost or deferred production.
Historically, treatments with liquid chemical inhibitors have been successful for those systems where the deposition occurs in the wellbore. However, traditional wellhead liquid treatments are not beneficial, if the deposition occurs beyond the perforations. There have been attempts to add liquid treatments during the stimulation process, but these have proved unsustainable because of the short treatment life, resulting in lost production and non-productive time (NPT).
However, hydraulically fractured wells can now be treated with slow-releasing, environmentally benign, proppant-sized solid inhibitors. The inhibitor is added to the proppant stages of the hydraulic stimulation, and serves to prevent and treat the deposition of scale and paraffin. The slow chemical desorption into the produced fluids—and the ability to select an inhibitor formulation tailored to the type of deposition—optimizes inhibition effectiveness and provides prolonged protection.
FLOW ASSURANCE CULPRITS
Although there are a multitude of factors that can lead to flow assurance issues, this article focuses on scale and paraffin. In the treatment of over 30,000 wells with this technology over the past 10 years, the majority of applications have been for scale and paraffin.
Paraffin. Under native pressure and temperature conditions, long-chain hydrocarbons (any chain length above 18 is termed paraffin) remain soluble in the reservoir, because they are at equilibrium with other reservoir fluids. During oil production, the reservoir equilibrium is lost, as pressure and temperatures are altered.
Driven primarily by changes in temperature, paraffin can deposit in the formation, near the wellbore, in tubulars and in surface flowlines and facilities. Continued paraffin deposition in the well results in decreased flow and leads to loss of production time, due to required well intervention.
Scale also can form as a result of changes in both temperature and pressure, and can cause issues during hydraulic stimulation, flowback and production. Scale formation during hydraulic stimulation can cause damage to equipment and consume fracture fluid chemicals. Scale deposition during flowback and production can damage the formation, interfere with artificial lift systems and increase uplift costs.
Historically, the industry applied liquid scale inhibitors into the stimulation to protect the pumping equipment. It has only been in the past 10-15 years that the industry has seen fit to apply scale inhibitors for prolonged, post-frac protection against scale deposition.
POST-STIMULATION TREATMENT OPTIONS
In the absence of adding a slow-release solid inhibitor during the fracture, the industry uses two means to ameliorate the issues related to scale or paraffin deposition. The most common types of treatments following stimulation are to: 1) use mechanical, chemical or thermal treatments to remove scale and paraffin depositions from the wellbore. For scale, it is common to apply acid, with or without a mechanical removal device, to solubilize and remove deposits. For paraffin, it is common to use thermal (hot water or hot oil), with or without a paraffin solvent, to remove deposits; and 2) immediately initiate treatment downhole with a liquid inhibitor. Typically, this is a continuously pumped application, or it can be done as a batch treatment using a treater truck.
Mechanical and thermal treatments can be expensive and may require the well to be shut in, sometimes for significant periods of time. For example, wireline cutting of paraffin is normally performed on a 10-to-30-day cycle. If thermal methods—circulating hot water or hot oil to melt, solubilize and remove accumulated paraffin—are used, the well must be shut in during treatment, and a thermally treated well often requires several days after treatment to regain pre-treatment production rates. In addition to cost and deferred production, treatments may be fleeting, because deposition can re-occur under given conditions. There is also evidence in the literature that indicates that prolonged thermal methods cause a buildup of high-molecular-weight hydrocarbons that are pushed back continuously into the formation, resulting in long-term damage.
Traditionally, liquid chemical inhibitors have been administered through batch, continuous or squeeze applications, to control the formation of scale and paraffin during oil and gas production. For a continuous, surface scale inhibitor application, each well requires equipment to pump the chemical from the surface to the bottom of the well. Such a system requires frequent oversight to maintain chemical application and equipment. The volumes of liquid inhibitor require containment to mitigate the risk of environmental impact in the event of a spill. Furthermore, because acidic scale inhibitors react quickly with carbonate formations, most inhibitors will precipitate near the formation face, providing only limited reservoir protection.
In sandstone, scale inhibitor adsorption squeezes are often performed in reservoirs, where a neutralized inhibitor pill solution can be pushed farther into the formation. However, small-to-negligible amounts of inhibitor are retained in the formation. A large fraction of these scale inhibitors flow back quickly, which results in insufficient long-term effective mitigation of scale deposition. Average cost for scale-related workovers in land applications can be as much as $100,000, plus a minimum of two weeks of downtime.
SOLID INHIBITOR ALTERNATIVE
The optimal fracturing chemical program inhibits deposition, to prevent flow assurance problems from the start of flowback and maximize production, both short- and long-term, in a cost-effective manner. Therefore, a preferred alternative to a remedial approach is a proactive one to avoid remediation. The optimal proactive chemical treatment is to add a solid inhibitor to the proppant stages during hydraulic stimulation. This methodology allows two treatments (fracturing and inhibition) to be combined, to save time and expense.
The solid inhibitor is placed far into the formation and is distributed evenly throughout the fracture with the proppant. Inhibition is provided long-term by the slow inhibitor release rate, and the entire fluid stream is protected. The solid chemistry is selective in nature and only elutes in the phase in which it is needed, making it both more effective and more efficient than liquid treatments.
A solid inhibitor that uses nonphosphonate, natural monomers has been developed and used to effectively control the formation of dissolved solids in several unconventional plays. The scale inhibitor is compatible with brines containing high volumes of total dissolved solids (TDS). It does not bio-accumulate, and has an excellent ecotoxicity profile for fresh and seawater species. Based on test results, the toxicological profile of this new scale inhibitor is comparable with polycarboxylates used in the food industry, and much better than the commonly used polyacrylate scale inhibitors, making it suitable for minimizing the environmental risk.
In 2005, this proppant-sized solid inhibitor, with a high surface area available for scale inhibitor loading by adsorption, was introduced for field application. The chemical that was placed on the substrate of the solid is the only active chemistry used. In contrast, the range of activity for a liquid inhibitor is typically 2% to 10%, by volume. So, while a liquid inhibitor must be diluted with solvents to be applied, the solid inhibitor contains significantly more of the active inhibitor molecule. Since the solid inhibitor was introduced, it has been used to treat more than 25,000 wells. The material has provided continuous inhibition protection for up to five years in low-water-producing wells, and for more than 1 MMbbl of cumulative water in high-water-producing wells.
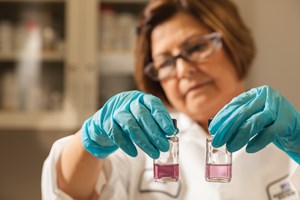
The solid inhibitor substrate is added on the fly, during proppant addition stages of the hydraulic fracture. To ensure even distribution of the solid throughout the proppant pack, the stimulation engineer calculates the addition rate of the proppant, and then of the solid inhibitor to track ramping up or down.
ANALYSIS AND PRODUCT SELECTION
For optimal treatment, recommendations and estimations on the quality of produced water, and potential scaling and paraffin issues, should be made prior to stimulation. Offset wells are used as the basis for estimations of what can be expected from the pending stimulation. Evaluation wells should be untreated wells in the same field and formation—and preferably at similar depth—as the recommendation. Verticals should be compared to verticals, and horizontals to horizontals. Samples should not be comingled. Oil and water samples are collected from these offsets and submitted to a laboratory for analysis, Fig. 1.
To provide a proper recommendation for a scale inhibitor, a complete water analysis (CWA) is performed to determine the total ion concentrations in the sample. Results are used in prediction modeling software to determine the likelihood and magnitude of scale. Dynamic scale tube blocking can be used to identify the most effective inhibitor chemistry to apply. This test also uses the CWA to generate a synthetic brine, to which inhibitor can be added as it passes through a tube. Pressure is measured to determine at what time in the test, scale forms with and without the added inhibitor.
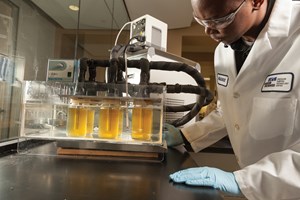
Complete oil analysis determines the percent of paraffin and asphaltenes in a crude sample, and provides a breakdown of the carbon chain length. This analysis can help determine the potential severity of paraffin deposition, if it were to occur in the system. Additionally, cold finger analysis testing aids in paraffin inhibitor product selection, Fig. 2. Oil samples are run through a test for forced precipitation of paraffin from both inhibitor-treated and untreated crude oil. By sample comparison, the most effective inhibitor for a given application can be chosen.
The data from these analyses are compiled and used to determine what inhibitors will be required, and at what concentrations. Field optimization and chemical efficacy are determined through post-job analysis and monitoring.
POST-JOB ANALYSIS
Assessing the effectiveness of chemical programs, including inhibition protection, calls for monitoring each chemical application on a prescribed schedule and using the monitoring data to determine whether the programs are performing to expectations. Managing the data, and its use in generating reports, is critical to the overall success of the program.
Treated wells should be sampled repeatedly for a predetermined period of time, with samples collected for pour points, cloud points, oil fingerprint analysis and scale inhibitor residuals. Successes and failures are compiled, and comparisons are made between treated and untreated well results. Failures are analyzed to determine if there are any unusual circumstances that can lead to the failure. Production data is pulled, to see if the well over- or under-performed. Chemical loadings are adjusted, depending on chemical life and well production.
Reports are used to inform of the status of the chemical treating programs. These reports contain the key performance indicators (KPIs) that reflect the requirements of the lease and the chemical contract. The detail and frequency of reporting are as agreed by the local team. The data generated from the monitoring programs and material deliveries are used to manage the chemical treating program. The data are used ultimately to determine the cost-effectiveness of the chemical treatments and potential optimization of the current
chemical program.
BONE SPRING FORMATION CASE HISTORY
An operator in the Permian basin, drilling into the Bone Spring formation, was experiencing flow interruption shortly after initial production. Samples of oil, water and solids collected from the well were submitted for testing. It was determined that both paraffin and scale posed a threat to the flow assurance of these wells. With the high initial production rate, it was not cost-effective to interrupt production, to apply a production chemical during this phase. For this reason, it was recommended to use a combination of solid, slow-release inhibitors in the completion of subsequent wells in this area.
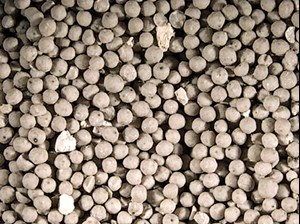
Cold finger testing was performed on depleted oil samples in a laboratory, to determine the best chemistry to decrease paraffin deposition. The crude samples were tested using variations of a suite of slow-release, solid, proppant-sized paraffin inhibitors at equal concentrations. The samples were conditioned and treated to reverse any paraffin precipitation that may have occurred at ambient temperatures. Baker Hughes’ ParaSorb 5000 inhibitor was selected and added with the stimulation at 500 lb per stage, to prevent the quick onset of paraffin deposition.
In addition to paraffin, producing wells in the formation exhibited barium scale deposition. The threat was confirmed through scale modeling software.
Barium sulfate is a common scale that is difficult to remove and can cost up to $250,000 for a horizontal well remediation, not including lost production. Based on the fracturing design and constraints, along with anticipated water production, the ScaleSorb 4 scale inhibition chemistry was recommended to inhibit scale threats for long-term effectiveness, Fig. 3. In combination, a loading of 350 lb per stage of the inhibitor was added.
Using this proactive chemical treatment program, the operator has treated more than 40 wells, and has had no paraffin- or scale-related failures reported within the first year of production. Health, safety and environmental exposure were minimized, and the cost of remediation and loss of production due to these deposits was mitigated.
- Shale technology: Bayesian variable pressure decline-curve analysis for shale gas wells (March 2024)
- What's new in production (February 2024)
- Prices and governmental policies combine to stymie Canadian upstream growth (February 2024)
- U.S. operators reduce activity as crude prices plunge (February 2024)
- U.S. producing gas wells increase despite low prices (February 2024)
- U.S. drilling: More of the same expected (February 2024)