Drilling Advances
It's quite fashionable these days to argue how the industry is close to constructing usable wellbores, using much of the same automated methodologies found in new-generation manufacturing plants. However, before equating the two, keep in mind that the designers of automated machines, stationed along a homogeneous assembly line, do not have to factor in the effects of transitioning from a reactive shale zone to a hard limestone stringer.
“We keep looking at other industries and see how automated they are, but when you bring in people from other industries and show them our challenges, they realize this [drilling automation] is far tougher,” said Robin Macmillan, senior V.P. at NOV. “Other industries don't require geological adaptability, which is one of the main challenges we face. So many things can change, and once an automated system has started, how will it deal with those changes?”
Geological adaptability is but one of the myriad technical and legal quirks that make the adoption of automated drilling systems appreciably more daunting than those of industries where repetition is mostly the norm, Macmillan suggested during the March Technology Forum of the IADC Drilling Engineering Committee (DEC) in Houston. A multi-disciplinary Joint Industry Project (JIP) has been wrangling with those issues, since it was formally established in late 2015 as a vehicle to fund and direct the Drilling Systems Automation Roadmap (DSA-R) initiative launched two years earlier.
The largely volunteer effort reached a milestone on April 6, with the long-awaited completion of the Stage One report, described as the first comprehensive draft detailing the work undertaken, to date. The integrated report was presented to representatives of 10 sponsoring companies, each contributing $10,000 to get to this point. Along with NOV, current sponsors of the cross-industry JIP include Exxon Mobil Upstream Research, Halliburton, Aramco Services, Occidental Petroleum, Shell, Total, Houston Mechatronics, Huisman and proNova TDE. Feedback from those companies will determine the next steps.
“The volunteer effort has taken us so far, but if we want to move this on, we need to grab someone and make this their job, and make sure they have nothing to do but drive this project,” Macmillan said.
Envisioned to provide the onshore and offshore industry a development pathway for automating the drilling process, the technology roadmap follows the widely accepted template developed by Sandia National Laboratories. Basically, this template provides a mechanism to guide advancement of automated drilling systems and “a framework to coordinate among disparate players.” Accordingly, one of the key drivers behind the DSA-R initiativewas eliminating the fragmentation that had different companies taking different paths “and keep everyone on the same page,” Macmillan said.
Filling in the blanks. That page, however, contains a number of blanks that must be filled in, ranging from agreement on universally accepted sensors to which entity bears liability, should something go amiss in an automated process.
“When we're looking to automate, for instance, we need to know what state we're in at the time. Are we drilling or are we tripping? For a machine, how do you define when one stops and another starts, and how do the machines talk to each other? These are all states that needed definition and we needed the JIP to decide how to do that,” Macmillan explained.
Among the multiple issues is what to do about the plethora of rig-based sensors, many of which deliver what can generously be described as questionable results. There is also the matter of how equipment from one company carries on an electronic conversation with equipment from another provider.
Settling on which sensors to adopt represents a significant hurdle, Macmillan said. “Anyone who's been on a rig knows what a challenge this is. Many rigs still have a paddle in the flowline, and we know how inherently inaccurate they can be. You go to a rig, and there may be six transducers measuring stand-pipe pressure. It looks like a porcupine with all the sensors hanging out if it,” Macmillan said.
“Everyone has a sensor, so whose sensors on the rig are we going to use? Who will calibrate the sensors, who will calibrate the calibrators, and how do we control all that?”
Most importantly, while an experienced driller can deal effectively with ambiguities and react to what the well is saying at any given time, not so with a computerized system. “Computers don't like ambiguous data. It's got to be precise,” he said.
Devising a standard language to enable inter-machine communication is also high on the to-be-determined list. “How does a piece of NOV equipment talk to a piece of Cameron equipment, and what sort of language are we going to need to get all those pieces of equipment talking to each other?” he said. “Do we need a standard and agreed-upon communication protocol?”
IP, liability issues. Though the project is intended to benefit the entire industry, when often competing companies are involved in developing the apps to actually operate the automated control system, intellectual property (IP) ownership will eventually come into play. “We have a bunch of companies working together, so does the IP [rights] belong to the operator, the contractor or the service company?”
Hand-in-hand with IP protection, liability issues must be rectified, especially as the industry puts more of the onus for well control on automated systems. “Next thing you know, we're going to have lawyers trying to work out who will be responsible if something doesn't work as perfectly as designed,” Macmillan said.
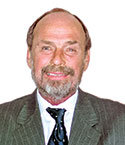