Challenging economics require drill bit improvements to lower break-even costs
The prolonged reduction in worldwide drilling activity has put a financial strain on service providers, but drill bit manufacturers continue to concentrate on refining technologies intended to increase penetration rates and overall tool durability. In spite of their relatively low cost, improvements in bit technologies have played a significant role in increasing drilling efficiency in both low- and high-cost environments. As manufacturers continue to develop and fine-tune PDC and roller cone technologies, in combination with enhanced drilling practices and application methods, operators are reaping the benefits of improved performance and lower global well costs.
HOLLISTIC DESIGN APPROACH
The Baker Hughes Talon Force line of PDC bits is designed to help operators improve ROP and distance drilled in high-speed vertical applications, and in long laterals through hard and interbedded formations. Since 2015, the bits have been run on approximately 1,800 wells and more than 7 million ft of hole section. The bits incorporate technologies to improve steerability, boost ROP in challenging environments, and increase consistency from run to run.
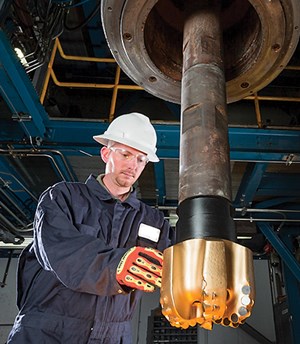
Developed using bit behaviors and responses as a whole, rather than just focusing on individual features, the technology platform leverages next-generation cutters and frame enhancements, to improve longevity while enhancing lateral and torsional stability, Fig. 1. Application-specific cutting structures and bit profiles promote optimized cutter loading while combining maximum aggressiveness and durability. Optimized blade layouts and unique hydraulic configurations contribute to increased mechanical efficiency and improved drilled cuttings evacuation.
Cutter technologies. Talon Force bits can be equipped with different types of cutters, depending on the application requirements. StaySharp cutters have delivered good results in curve and lateral intervals improving ROP by up to 40% in Eagle Ford shale wells. The shearing elements are manufactured, using the latest HPHT diamond synthesis process to deliver superior wear resistance, toughness and thermal stability. Additionally, a new 1-in. cutter is now available that increases drilling speed in soft formations by maximizing depth-of-cut.
For hard, interbedded formations, Stabilis reinforced cutters are the preferred tool. The cutters’ modified geometry enables them to withstand three times the load of a conventional design. The cutter reduces torsional oscillation, providing a much smoother torque response than standard cutter geometry. In the Wolfcamp formation of West Texas, bits with the new cutters have reduced drilling time up to 36%, while improving ROP by 25% and drilling up to 55% more footage, compared to standard PDC bits with chamfer cutters. In Saudi Arabia, these cutters have improved footage by up to 60% and reduced drilling costs as much as 9%.
Kymera XTreme. The new Kymera XTreme bits build on the success of prior hybrid technology to deliver smooth, fast and more durable drilling performance—in both vertical and curved hole sections. Engineers have balanced the dynamics of the roller cones and PDC blades, mitigating downhole vibrations and increasing durability. As a result, the new bits deliver more reliable toolface response and smother drilling in difficult environments, including challenging carbonates and interbedded formations.
The bit’s optimized torque response enables it to maintain verticality when needed, yet still deliver high build-up-rate capability, when required, for maximizing pay zone access, making it an efficient solution for drilling both the vertical and curve. With more than 70 unique designs and 13 different bit sizes, ranging from 8½-in. to 26-in., customized sizes for this hybrid bit are offered for many specific applications.
Case study. In the Middle East, the hybrid bit was selected for a challenging deep-gas operation. Issues in previous vertical sections included risk of losses, and very hard and abrasive formations. Additionally, roller cone performance delivered slower-than-desired ROP. The operator ran the new hybrid bit and drilled the section in one run, shoe-to-shoe, reducing tripping time and the cost of a new bit. After that run, an analysis revealed that the new bit technology improved ROP by 173%, and reduced cost/ft by 7%.
ADVANCED MODELING PROCESS
If the goal for drilling is to improve efficiency on every well, then a heavy emphasis on simulation is key. By more accurately modeling bit performance, Halliburton Drill Bits and Services is helping operators make better choices about which cutting structure to use, which technologies will improve dull condition, and what operating parameters should make the bit perform better than on the previous run.
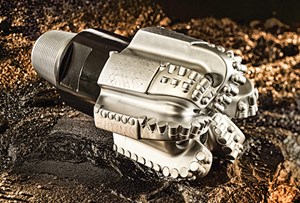
GeoTech PDC. To achieve this goal, GeoTech fixed-cutter PDC bits were launched, aiming to maximize ROP on longer drilled intervals, Fig. 2. The product line introduces a new rock interaction model, which moves away from the industry-standard force-balancing models. The new simulation process breaks down how chipping, crushing and shearing of the formation by the PDC cutters changes in different rock types and strengths. In addition, the changes in the bottomhole pattern made by the cutting structure on preceding rotations is analyzed, to provide more accurate interpretations of engagement of the cutters into the rock. These changes deliver a drilling model more capable of simulating real-world performance that will be encountered in an ensuing well.
Modeling identifies opportunities. This more-accurate model provides design engineers a better understanding of the downhole environment, enabling them to sustain the desired conditions, using optimized bit technologies. Unique depth-of-cut control elements, placed in optimum locations, stabilizes drilling conditions, so the PDC cutters drill with maximum efficiency, given the energy available to them. By reducing torque variations and limiting axial vibrations, the cutting structures incur less damage and are more likely to drill in an efficient manner, as predicted by the simulation.
However, no new PDC product would be complete without improving its shear cutting elements, and the GeoTech line is no exception. Specific cutting structure layouts, combined with application-specific cutters, have delivered up to 50% improvement in abrasion resistance, and are 20% more resistant to chipping/spalling. The aim is to keep the cutters sharp, to maximize efficiency throughout the run. From a drill bit perspective, the ultimate goal is to select/apply the right technology, in the right application, with the right operating parameters.
Design at the customer interface. The DatCI design process starts by incorporating input from the operator to guide development. Next, the drilling team draws from an extensive assortment of analytical tools that include simulation, analysis and design software programs. The output provides an in-depth understanding of what the operator expects, in terms of performance improvement, and helps select the appropriate technology to achieve the goals. The continuous learning cycle enables the DatCI groups’ application experts to improve drilling efficiency and lower drilling costs for operators around the world.
ANALYSIS AND OPTIMIZATION
Tektonic drill bits from National Oilwell Varco (NOV) are designed to increase drilling efficiency by maximizing ROP, durability/stability, and directional control, Fig. 3. Tailored for specific operations using proprietary dynamic rotation bit modeling and advanced fluid flow software, the bits are designed to improve transient bit-rock interactions, minimize frictional losses, improve cutter load distribution and maximize cuttings evacuation.
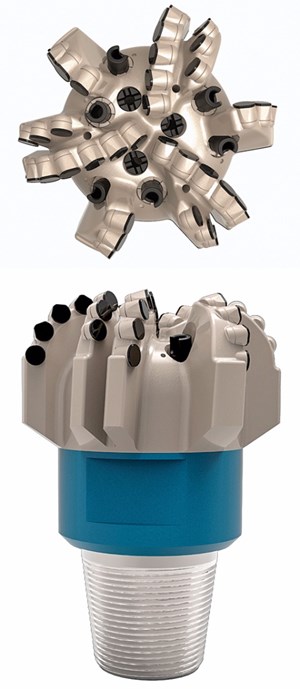
NOV’s engineering team has developed specific design requirements to enhance understanding when drilling in hard rock and carbonate applications. Application challenges include high formation ductility, high rock strength, interbedded lithology and thermal degradation of cutters. When drilling interbedded formations, the alternating rock strengths increase the potential for lateral, torsional and axial vibrations, which can damage the cutting structure. These problems can reduce ROP and durability, requiring additional runs to complete the hole section.
Developing core technologies. Following the studies that led to the development of advanced design guidelines in the above applications, NOV’s R&D team created three new improved technologies: 1) Reflektor 3D cutters; 2) new cutting geometries; 3) optimized nozzle placement for primary cutting structure and a dedicated flow path for secondary cutters.
The new Reflektor 3D cutters, used in combination with standard cutting elements, create maximum efficiency, fracturing and shearing both hard rocks and ductile carbonate formations. However, the 3D cutters are most effective in clastic formations, including sandstone, siltstone and claystone, as well as carbonates, such as chalk, limestone and dolomite.
The cutter geometry increases stress concentration in the rock, making the bits suitable for drilling in formations with higher stress requirements. The cutters create cracks that propagate to the surface, generating thin cuttings that require less energy to fail.
New nozzle configurations prolong bit life by cooling and cleaning the primary cutting structure while mitigating the potential for thermal damage to the cutters. The dedicated flow paths optimize hydraulics to the secondary cutters. The R&D team used advanced CFD/FEA analysis, and more than 40 pressurized full-scale drilling tests, in addition to field tests, to evaluate the findings.
Case studies. In Oman, a major operator drilled a 12¼-in. vertical section with a 66-type bit on a rotary assembly through an abrasive sandstone. Performance was good, and the bit drilled 2,607 m of formation at an ROP of 15.4 m/hr, setting a new field record.
During another run in Oman, an operator used a 12¼-in. 66-type bit to drill a section from shoe to TD through highly abrasive sandstone. The bit successfully completed the entire hole section in a single run with a field record ROP of 23.4 m/hr over the 2,408 m interval.
Using a 14¾-in. 76-type PDC bit, a major operator saved several trips, and achieved higher ROP, drilling through hard carbonates and chert in the Carnarvon basin, Australia. The bit drilled 1,794 m of formation at 57% higher ROP than the offset average of 29 m/hr.
PDC DRILL-OUT BIT
Historically, operators have used standard PDCs and roller cones to mill frac plugs and various types of completion equipment. However, most PDC bits used in milling operations are engineered with traditional design concepts optimized for drilling formation. This creates a problem, because performance metrics for drilling frac plugs are significantly different than those used for drilling formation. When penetrating rock, maximizing ROP is highly advantageous, but with frac plugs, increased cuttings size associated with fast drilling makes high ROP undesirable. In many cases, the traditional approach to optimizing PDC bit designs is contrary to what’s best when drilling frac plugs.
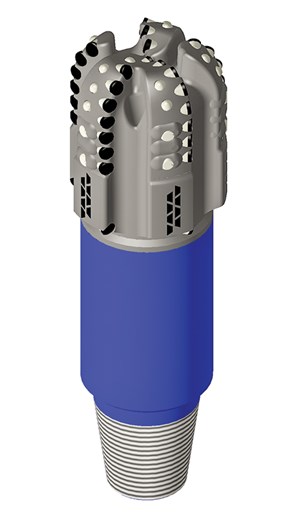
To solve the predicament, PDC Logic introduced FracDrill PDC bits that feature application-specific body geometry and design features to specifically address challenges encountered during well completion and intervention operations, Fig. 4. The bits have a reduced cutter size, smooth torque response, and robust cutting structure, compared to standard fixed-cutter products. The fit-for-purpose drill-out bit is equipped with intelligent design features, to manage drilled cuttings size, reduce torque, and increase cutting structure durability. This combination of technologies enables the bits to consistently complete drill-out of all stages in a single run. In field applications, the bits have successfully reduced NPT, drilling relatively simple cast iron ball-seats to the most challenging, composite frac plugs.
Case studies. In the DJ basin, the bit was used in a drill-out operation to overcome inefficiencies where the junk mills were sustaining heavy wear and being pulled undergauge. A 3¾ -in. drill-out bit was run and completed two consecutive jobs, drilling a total of 70 composite frac plugs in just 7½ drilling hr, averaging a fast 6.4 minutes/plug. The offset junk mill run was graded 3/16-in. undergauge after close-up drilling only 35 plugs, while the FracDrill bit was pulled in gauge and dull graded 1-1 after completing back-to-back wells.
In the Eagle Ford shale, the bit improved the drilling efficiency of not only the frac plugs in their 21-23 stage count laterals, but also in sand/proppant removal between stages. The bit saved an operator an estimated $50,000 on one completion by reducing drilling and washdown times by approximately 75%.
PRECISION ROLLER CONE BIT
Rubicon Oilfield International is a new company, but through acquisition, it has over 40 years of experience manufacturing specialized drilling products. To create a differentiable product to service the growing frac plug drill-out application, the company launched its Production line of premium roller cone bits, Fig. 5.
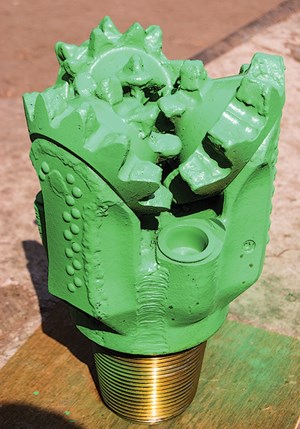
Rather than just shrinking an existing bearing to fit in a 4½-in. bit, the design team used a practical innovation approach to ensure downsize engineering would produce a fully optimized bearing for challenging drill-out applications. The precision machined package is manufactured with proven wear-resistant materials, designed to withstand heavier loads than conventional hard materials used in standard bearings. They are machined to ultra-high tolerances, to deliver consistent performance, and are protected by unique V-Ramp seal technology. The seal’s unique configuration reduces lateral movement and provides consistent contact pressure around the circumference, to ensure that harmful contaminants do not invade the bearing system.
Additionally, a unique tooth layout enables operators to mill plugs more effectively, and produces smaller cuttings that can be completely evacuated before completion, to ensure they will not inhibit production flow, when the well is completed.
Case study. The new 4½-in. P21 design was used on five wells in South Texas by two different operators on 330-550 RPM motors, with good results. The frac plug drill-out times on one well averaged less than three min. per plug (20 plugs). Even the slowest plug drilling time was just slightly higher than the offset average of nine min. (27 plugs). The bit was pulled in excellent dull condition. In other applications, the bit has regularly recorded efficient drill-out times, irrespective of the type of plug being milled. Rubicon is also working on a smaller-sized Production roller cone bit, which will be released in the coming months.
RIDGED DIAMOND ELEMENT BIT
With the introduction of three-dimensional cutter technology (3DC), Smith Bits, a Schlumberger company, has developed new PDC designs that withstand the toughest formations and downhole conditions. The increased durability of these new cutting structures are ideal for a range of drilling conditions, such as long-interval drilling in abrasive formations, and in hard carbonates that contain chert and pyrite inclusions.
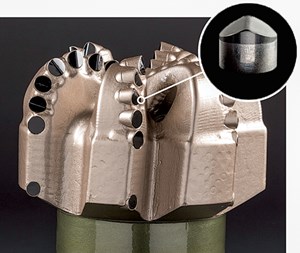
The latest 3DC introduction is the AxeBlade ridged-diamond element bit, Fig. 6. By incorporating Axe ridged diamond elements across the bit face, designers have developed a bit optimized for a wide range of formations, which can improve ROP and steering response in directional applications. The elements have a distinctive shape that combines the shearing action of a conventional PDC cutter with the crushing action of a tungsten carbide insert in roller cone bits. The unique geometry drills rock more efficiently, achieving 22% deeper penetration and generating wider grooves than conventional PDC cutters. The ridge-shaped geometry yields a diamond table that is 70% thicker than a conventional cutter and provides higher impact resistance. The new bits reduce reactive torque in deviated applications, improving directional control compared to conventional PDC bits equipped with conventional cutters.
Case studies. In the Anadarko basin, the new bit was used to drill a well’s intermediate interval from 5,918 ft to 9,047 ft in a single run at an ROP of 95.54 ft/hr. The bit increased ROP by 27%, compared with bits used in an offset well. Additionally, under similar drilling parameters, and using the same cutting structure layout, the new bit generated 20% less surface torque, saving the operator 14.75 hr of rig time.
In the Williston basin, Continental Resources used the new bit to drill an entire 15,340-ft lateral in a single run, in 113.5 hr. The performance set a record for the longest lateral section drilled by a 6-in. bit in the Bakken shale. The bit/BHA completed the lateral in fewer hours than the combined time required for two runs on the previous well, not including 24 hr saved in trip time. In addition, the new-type bit required only 912 ft of sliding compared with the two offset bits, which, combined, required 1,213 ft of sliding. On a subsequent run, the bit set another 6-in. footage record in the Bakken shale, drilling 15,375 ft of lateral hole section in 113.5 hr.
PDC BITS FOR RSS APPLICATIONS
Ulterra Drilling Technologies has updated its line of PDC bits, optimized for use with assemblies equipped with rotary steerable systems (RSS). Increasingly, the viability of these directional drilling tools have been recognized in many U.S. land plays. To extract the full potential of different RSS types, operators have sought out drill bit manufacturers, to provide designs tailored to specific parameters and BHAs.
A specific RSS, fitted with a customized PDC bit, set several new records for a service provider in the Eagle Ford shale. The BHA averaged more than 16,000 ft per run in three wells, drilling at an ROP of 87 ft/hr. In one application in Live Oak County, Texas, the bit set footage records for the type of RSS applied, drilling 16,234 ft. The extended-reach well had a TD of 22,700 ft, and achieving the lateral distance was a big challenge yet it was accomplished, using one BHA and staying on bottom for 192 hr.
Unique cutter configuration. The company has utilized its proprietary technology to develop CounterForce PDC bits, designed specifically to reduce lateral vibrations, a leading cause of downhole tool failure, Fig. 7. The cutters are aligned with alternating side rakes to keep the bit from over-engaging, producing a more consistent torque response that allows drillers to be more aggressive when applying operating parameters.
In Abu Dhabi, the bit was used with another type of RSS to help solve lateral vibration issues that were causing downhole tool failures. The operator’s engineering team lead said that the bit allowed the rotary steerable assembly to drill 824 ft to section TD, at an ROP of 23 ft/hr. The run was 66% faster than the average of the two previous bit runs in the mother hole. It also was 230% faster than the average of the two previous bit runs in the pilot hole. This increased performance saved the operator the expense of three trips.
Additionally, an engineering analysis revealed that the tailored PDC bits, optimized for an operator’s specific well plan, reduced downhole tool failures 62%, compared to other types of PDC bits run on the same RSS tool. The increased performance has influenced operators to run the bits on high-profile RSS, in a growing number of basins, formations, and drilling applications.
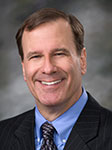
- Regional Report: Which future for Marcellus and Utica shales? (November 2024)
- Sustainability: Meeting new drilling demands with smarter power management (November 2024)
- Shale technology: Using expandable casing patches to reinforce well integrity (November 2024)
- Novel approach of recovering energy from high-pressure multiphase streams (November 2024)
- Drilling advances: Is it always only about people? (November 2024)
- Digital control architecture optimizes plunger lift wells (November 2024)