As more resources are dedicated to mending ailing balance sheets, the development of new technologies for future requirements has, largely, taken a backseat. At least one consultant, however, sees serious repercussions afoot, as well pressures continue to increase with approaching bottomhole temperatures (BHT) that could make areas like the Gulf of Thailand’s notorious “ring of fire” seem like a lukewarm bath by comparison.
“There is definitely a gap and lack of commitment to (providing) the resources, the funding and the time to get R&D development going in HPHT (high-pressure, high-temperature),” said Debbie McIntosh, head of subsurface and wells practice for UK-based OTM Consulting. “People believe that pressures and temperatures will continue to rise. The current short-term focus will lead to higher costs down the line,” she said.
To illustrate, she pointed to industry surveys where respondents see future operational boundaries peaking at between 20,000-psi and 30,000-psi pressures. “What is interesting is that we had some people (forecasting) right up to 50K (pressures),” she said. As for impending BHT, future operational boundaries up to 500°F are in the offing, far from the current baseline of 300°F–350°F, McIntosh said in a presentation at the September World Oil HPHT Drilling, Completions and Production Conference in Houston.
Noting that the majority of HPHT wells, to date, have been drilled in North America and Europe, she said other areas are “catching up,” with sour wells also joining higher pressures and temperatures. “We’re seeing increasing challenges in combining higher pressures and temperatures with corrosive environments,” she said.
Current gaps. In 2013, well control and intervention were identified as the primary issues in HPHT developments, but two years later, materials and downhole electronics emerged as the most glaring deficiencies. “There’s been a lot of attention on rectifying the materials issues, but a lot less on the electronic and sensor issues,” she said. “Much of the talk had centered on wellhead design, but actually we can meet the current needs quite well. By contrast, there is a huge lack of reliability in directional drilling equipment, which brings us back to the challenges of downhole electronics.”
McIntosh said the results of an OTM survey conducted in late summer, showed nearly 80% of the 50 or so players petitioned believed that the current level of investment will not meet the future requirements, with the blame, of course, falling squarely on low commodity prices. Considering the lag time between conception and commercialization, the industry already is well behind the eight ball, she said.
“Low oil prices are the bane of our lives at the moment, but we don’t have time to wait. We have to already start looking at accelerating technology programs to meet the requirements we will have in 10 years’ time,” she said.
McIntosh said early collaboration between the technology developers and end-users, and standardization, will go a long way toward increasing accessibility, while improving reliability and lowering costs. “We also need to expand R&D to collaborate with other industries, such as space, military and pure scientific research agencies. There definitely are technologies in use that, under different applications, could perform the way we need them to,” she said.
Looking outside. As evidence, the Oil & Gas Innovation Center, Inc., of Palo Alto, Calif., has identified nearly 350 cross-over technologies that are commercialized, “or on the cusp of being commercialized,” that have potential applications in the oil and gas sector, said CEO and founder John Barratt. “We’re talking $2-to-$3 billion worth of technologies developed with someone else’s money,” he told the HPHT conference.
Barratt, whose company scopes out external technologies for oil and gas applications, cited, as an example, a recent development in the high-temperature space environment that he said comes close to addressing the 500°F BHT threshold that McIntosh referenced. Specifically, he pointed to what he referred to as a temperature hardening device, comprising an electron-charged collection plate installed beneath the industry-standard, complex metal oxide semi-conductor (CMOS). By reducing substrate resistance, the technology has demonstrated sustained operation at 392°F, with indications that it could extend past 482°F, he said. “There’s obvious downhole applications for technologies like this. What’s cool is that it not only allows sustained operation at high temperature, but you do not have to re-design the circuitry,” he said.
The oft-questioned reliability of elastomer seals under elevated temperatures likewise could possibly be addressed with an externally developed concept that untangles carbon nanotubes to improve elastomer resistance. Barratt explained, “Carbon nanotubes can certainly change the characteristics of elastomers. But, when you produce these things, they get tangled up like cotton balls, which kind of ruins their functionality. This company has essentially separated the carbon nanotubes, and once they are untangled and functionalized, you can put on a coating and incorporate them in a variety of elastomers to change the abrasion resistance and the tensile characteristics. There’s a variety of characteristics you can change.”
Another cross-over candidate is a new vibration-resistant fastener, originally developed by a physician for spinal implants and since put to use in the aerospace industry, which Barratt said “can readily be brought into this industry for high-vibration applications.”
“If you can access somebody else’s technology through some kind of licensing arrangement or some kind of creative marketing agreement, that’s a tremendous advantage. And, looking at the technology developed in other industries, you’ll be surprised at the level of creativity that will inspire within your own shop,” he said.
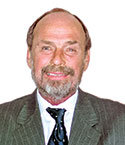
- Regional Report: Which future for Marcellus and Utica shales? (November 2024)
- Sustainability: Meeting new drilling demands with smarter power management (November 2024)
- Shale technology: Using expandable casing patches to reinforce well integrity (November 2024)
- Novel approach of recovering energy from high-pressure multiphase streams (November 2024)
- Drilling advances: Is it always only about people? (November 2024)
- Digital control architecture optimizes plunger lift wells (November 2024)